How a Flatbed Applicator works
Save up to 80–85% production time
Manual vinyl application and mounting of self-adhesive vinyls and laminating work are commonly and skillfully performed around the world. However, a mistake in handling the material or a moment of lost focus when applying pressure could waste the job and incur unwanted costs. The time required for manual production is excessive compared to the semi-automated laminating process offered by the new CWT Worktable Flatbed Applicators. The estimated reduction in production time is up to 80–85%!
Better Profit and Better Health
A potential cost saving is maintaining operators’ health and physical status through improved user ergonomics that the Flatbed Applicator technology offers. Intense manual effort over time can often cause fatigue-related injuries. Beyond the cost issue, the temporary leave of a skilled employee can be crucial to the company.
Fast Assembly and Environmentally Friendly Logistics
The modular design makes the CWT Worktable easy to transport and install. The units are delivered in compact packages, less than half the volume of those from other suppliers. Beyond the low transportation cost, the slim package can easily be brought inside customers’ facilities through standard-sized doors. Our flatbed applicators can be accessed anywhere.
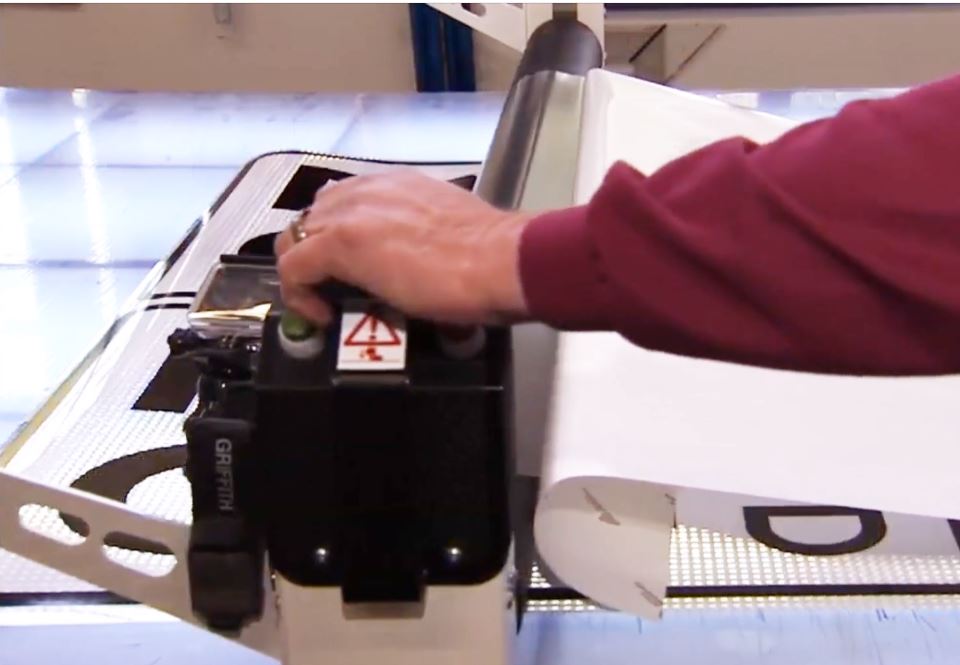
Easy to learn and operate
Working with a quality flatbed applicator is easy to learn, and you don’t need to hire specially skilled staff to operate it. With the high output and quality you can achieve, it will elevate your competitive level and make your job more enjoyable.
In our range of flatbed applicators, from the smaller Advantage series to the fully equipped Premium series, you can find the right flatbed applicator to meet your demands and the specifications given by manufacturers of vinyls and protective films, such as meeting their warranty terms.
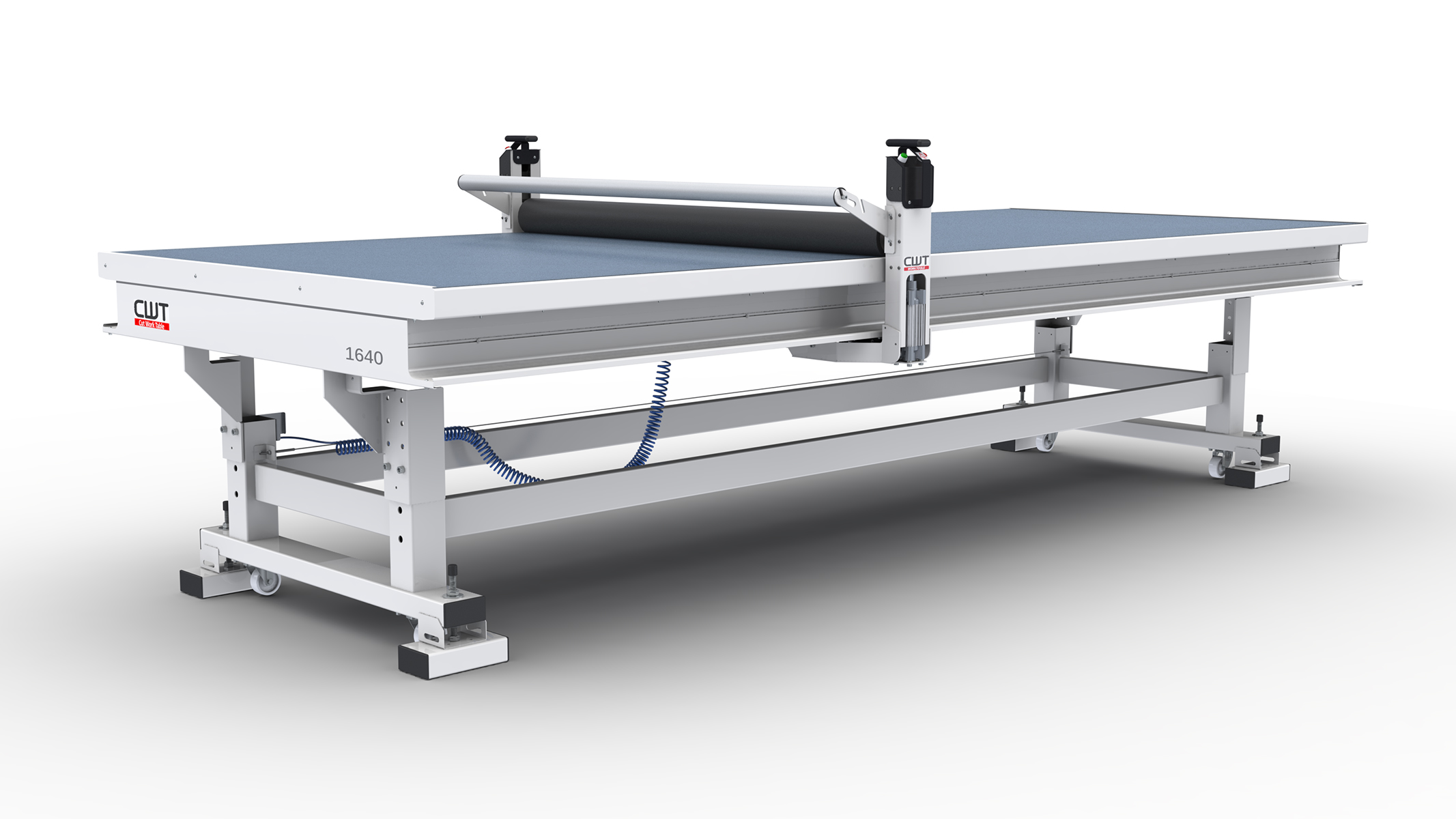
Full control over the laminating process
When using a flatbed applicator, you will have full control over the laminating process, and you can do it all by yourself. Place whatever substrate you want to laminate on the table, then position your graphics on top of it. Once you lower the roller to press it together, it won’t move, and you don’t have to worry about messing up expensive material with wrinkles and bubbles. However, always clean the surface thoroughly before exposing any adhesive. The easiest way to do this is to use our Sticky Cleaner Roller.
Whether you are working on banners, acrylic sheets, folded aluminum sheets, or even making your own mixed material sandwich panels to bring to your router, the versatility of these machines means you will almost always find a way to do it.
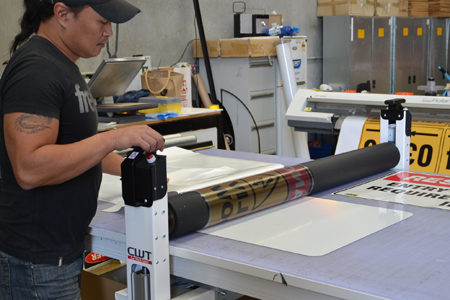