Traffic Sign and road sign production: A Comprehensive Guide to Using CWT Flatbed Applicators
The production of traffic and road signs is a critical component of modern infrastructure, requiring precision, durability, and adherence to industry standards. Over recent years, advancements in digital printing and flatbed applicator technologies have transformed the manufacturing process, offering unprecedented levels of efficiency and quality control. This guide explores the benefits and applications of CWT flatbed applicators in traffic sign manufacturing, detailing how these tools streamline production and ensure high-quality output.
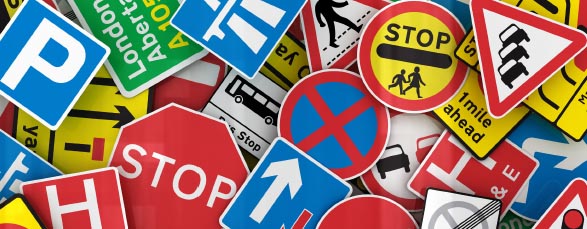
The evolution of traffic sign manufacturing
From manual to digital
The shift from traditional manual processes to digital solutions has marked a significant turning point in the sign-making industry. The first digital printing system specifically for traffic signs was introduced in 2006. Today, manufacturers utilize advanced inkjet UV, Traffic Jet and latex printing technologies that provide consistent quality at a lower cost. These digital solutions have paved the way for more efficient and flexible production capabilities.
The role of Flatbed Applicators
Flatbed applicators have become essential in applying reflective sheeting, overlay film and laminate to sign substrates. They offer precise control over the application process, improving both the speed and accuracy of sign production. The introduction of semi-automatic flatbed applicators represents a major leap forward, allowing manufacturers to optimize their workflows and meet the growing demands of the industry.
Why choose CWT Flatbed Applicators?
Key advantages
- Efficiency: CWT flatbed applicators reduce production time by up to 85%, allowing a single operator to manage large volumes of work efficiently.
- Precision: The applicators ensure millimeter accuracy in cutting, mounting, and laminating reflective sheeting.
- Versatility: Suitable for a wide range of substrate types and thicknesses, accommodating both small regulatory signs and large traffic guide signs.
- Quality Control: Features advanced controls for pressure, heat, and speed, ensuring a consistent, quality-controlled application process that meets the high demands of reflective film manufacturers.
Building a road sign manufacturing workstation
Essential components
- CWT Flatbed Applicator: The core of your workstation, providing the tools needed for efficient sign production.
- Digital printers: Incorporate inkjet UV or latex printers to produce high-quality reflective films.
- Reflective sheeting, laminate and overlay films: Choose materials that comply with industry standards for durability and visibility.
- Support materials: Use polystyrene or custom jigs to support hollow, box-shaped substrates or for substrates with brackets or rivets during the application process.
- CWT accessories: Include guide sign jigs, linear cutters, roll holders, cleaning rollers, and other tools to enhance functionality and productivity.
Step-by-Step Guide to Traffic Sign Production
Step 1: Prepare your work area
- Clear the space: Ensure the CWT flatbed applicator is on a clean, flat surface. Remove any obstacles around the work area.
- Prepare your materials: Have your self-adhesive vinyl, prints, and substrate ready.
Step 2: Position the substrate
- Center the substrate: For thicker materials that rise from the glass bed, center the substrate on the worktable. If placed on one side, counterbalance it by placing material of the same thickness on the opposite side. This ensures the roller hits evenly when lowered and pressurized.
- Support hollow substrates: Use your polystyrene or custom jigs to support hollow, box-shaped substrates or for substrates with brackets or rivets during the application process.
Step 3: Apply reflective sheeting
- Align the sheeting: Position the reflective sheeting accurately on the substrate.
- Lock in place: Lower the roller about 30 cm (1 ft) from one end to secure the sheeting in place.
- Remove backing: Flip the short end of the reflective sheeting over the roller and remove the release liner or backing paper. Cut off or fold the backing paper, leaving about 15 cm (5-6 in) against the roller. If cut, fold the backing paper downward to form a straight fold to prevent dust from sticking to the glue.
Step 4: Mount the reflective sheeting
- Smooth application: Move the roller over the substrate, applying the reflective sheeting evenly. For thicker substrates, use a similar thickness at the end to prevent the roller from falling off the edge.
- Continue application: Lift the roller where the backing paper is cut off.
- Turn the remaining part of the reflective sheeting over the roller.
- Grab the folded backing paper, pull it upwards over the roller, and hold it while moving the roller over the remaining part of the substrate. Ensure the reflective sheeting is centered and straight over the roller and let the backing paper release just on top of the roller.
Conclusion
The use of CWT flatbed applicators in traffic sign manufacturing offers a significant competitive advantage, delivering efficiency, precision, and quality control. By incorporating production technology into your production line, you can meet the demands and standards of the industry while optimizing your workflow and reducing costs.
Industry insights
As the industry continues to evolve, the integration of digital printing and flatbed applicator technologies will remain crucial for staying ahead. By adopting these solutions, manufacturers can enhance their capabilities, meet increasing demand, and ensure the production of high-quality traffic signs that meet all regulatory requirements.